Process Hub For The Production And Service Business
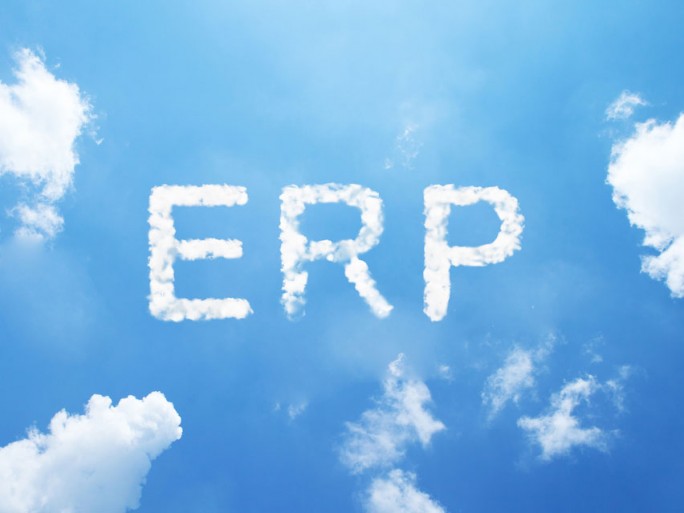
An ERP system should support, control and monitor all processes involved in the handling of repairs and services.
Many medium-sized companies with their own production facilities are constantly expanding their service business. However, the ERP system is not always up to the task – what works well in production reaches its limits in after-sales support. “The service business with spare parts and services requires special features in an ERP system, which often follow the production model in terms of discount scales or warranty services, but require significantly different processes in some areas,” says Christian Biebl, Managing Director of Planat.
ERP as a process hub for production and service
In addition to purchasing, sales, production and all other areas, service order processing, workshop control, spare parts sales and shipping play an essential role in ensuring smooth day-to-day operations. The optimal ERP system supports, controls and monitors all processes that are relevant to the processing of repairs and services. Thanks to mobile working time recording and mobile CRM access via app, employees in the field can be directly connected to orders, and full transparency of individual orders is provided at all times. “With our specialization in medium-sized manufacturing companies, we don’t see the need for individual stand-alone solutions for production and service, for example, but rather view the ERP system as a common hub that controls all processes related to both business models. In this way, we give our customers the opportunity to optimize sales potential in both business sectors,” explains Christian Biebl from Planat
In addition to purchasing, sales, production and all other areas, service order processing, workshop control, spare parts sales and shipping play an essential role in ensuring smooth day-to-day operations. The optimal ERP system supports, controls and monitors all processes that are relevant to the processing of repairs and services. Thanks to mobile working time recording and mobile CRM access via app, employees in the field can be directly connected to orders, and full transparency of individual orders is provided at all times. “With our specialization in medium-sized manufacturing companies, we don’t see the need for individual stand-alone solutions for production and service, for example, but rather view the ERP system as a common hub that controls all processes related to both business models. In this way, we give our customers the opportunity to optimize sales potential in both business sectors,” explains Christian Biebl from Planat.
Shared master data simplifies processes
Shared data management enables increased process effectiveness and transparency and the precise deployment planning of human and material resources. With the ERP system as a central anchor, the important customer, partner and product master data is also on a common level, which can be accessed by all departments at any time. “The central data storage in the ERP core helps to be able to optimally respond to the needs of the customers across the company. In today’s competitive environment, it is not just product quality and value for money that companies can score points with, but above all the service quality and speed with which customer problems are handled and solved. And this is especially true for medium-sized businesses, which under the current circumstances must particularly protect their competitiveness,” describes ERP specialist Christian Biebl.