Hödlmayr Optimises Internal Vehicle Logistics Processes
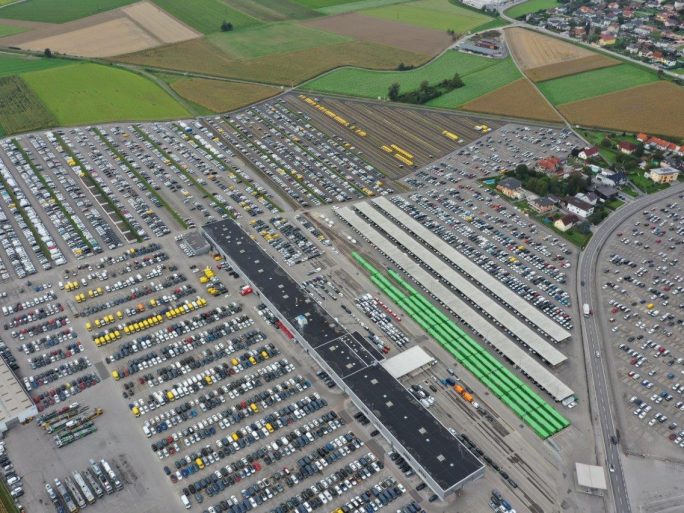
Continuous digitalisation of internal logistics processes for around 500,000 vehicles per year.
For the areas of yard and workshop management, the Austrian vehicle logistics expert relies on the “Syncotess” solution from the Aachen-based software company “Inform”. The new systems, which are based on operations research and artificial intelligence, replace the Austrian family-owned company’s previous in-house developments. Optimisation algorithms and AI processes will recalculate every second which tasks need to be carried out with which resources, where and in which order, so that the respective location operates optimally.
Automatic scheduling
At Hödlmayr, the algorithms will in future take over, for example, the allocation of vehicle movements to employees, the selection of parking spaces and the sequence of orders to be processed in the repair shops. This automatic scheduling takes place in a central control centre on the basis of the rules defined for each location. In addition, media discontinuities are avoided since data from all relevant sources converge in the solution. This enables Hödlmayr to manage by exception. The dispatchers only intervene in special cases, yet for their part they have a holistic transparency of the condition and status of each vehicle and order.
Hödlmayr specialises in the entire supply chain of vehicle logistics, from the takeover of vehicles ex works or port of entry to delivery to the fleet owner, vehicle dealer or end customer by means of home delivery. With around 600 vehicle transporters and 20 block train systems, the company operates one of the largest transport fleets in Europe. In 12 vehicle logistics centres, the company stores, maintains, checks, services and modifies new and used passenger cars, commercial vehicles and agricultural machinery.